Hydraulic hoses are classified primarily by their construction and reinforcement, determining their pressure ratings, flexibility, and durability. The classification is usually done according to industry standards such as SAE (Society of Automotive Engineers) or ISO (International Organization for Standardization).
Single-Wire Braid Hoses (e.g., SAE 100R1): These hoses have a single layer of steel wire braid for reinforcement, making them suitable for medium-pressure applications where flexibility and moderate strength are required.
Double-Wire Braid Hoses (e.g., SAE 100R2): These hoses feature two layers of steel wire braid for enhanced strength and durability, designed to handle high-pressure environments and heavy-duty applications.
Spiral-Wire Hoses: These hoses use multiple layers of spiral-wound steel wire for extreme pressure and flexibility requirements, typically used in very demanding hydraulic systems.
R1 hoses have a single-wire braid reinforcement and are suited for medium-pressure applications, while R2 hoses feature a double-wire braid for higher pressure and increased durability.
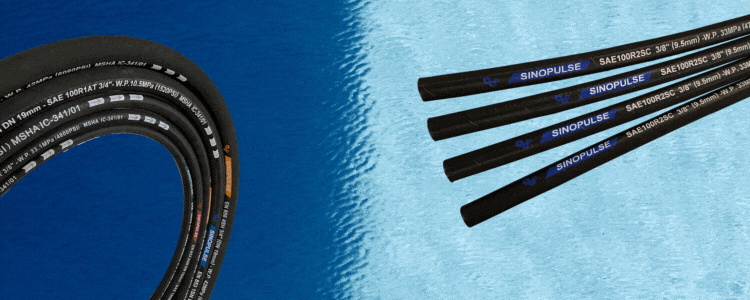
SAE 100 R1AT One Steel Wire Braided Hose
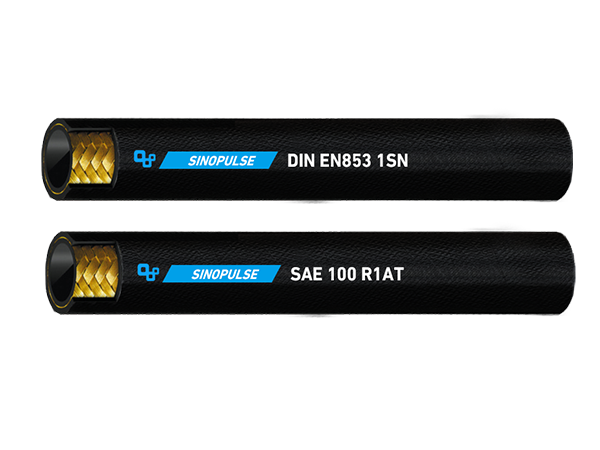
SAE 100R1 single wire braided hose is a typical high-pressure hydraulic hose suitable for hydraulic lines or general industrial systems. One wire braided hydraulic hose is made of oil-resistant synthetic rubber lining, one wire braided reinforcement material and oil, fuel and wear-resistant rubber cover. High tensile strength wire reinforcement material enables SAE 100R1 hose to support higher pressure than ordinary steel wire.
SAE 100R1 rubber hose should be used with petroleum and water-based hydraulic oils in the temperature range of -40°C to +100°C.
Single Wire Braid Hoses (e.g. R1): These hoses feature a single wire braid reinforcement, making them suitable for medium pressure applications where flexibility and moderate strength are required.
- Inner Tube: oil-resistant synthetic rubber.
- Reinforcement: one braid of high-tensile steel wire.
- Cover: weather- and oil-resistant synthetic rubber.
Temperature Range: -40℃ to +100℃.
Main Applications: Used for conveying low-medium pressure of oil- or water-based hydraulic fluids.
Standards: ISO 1436 R1AT, SAE J517 100R1 type A or AT
Advantages of using R1 hose:
Cost-effective: Typically less expensive than high-pressure hoses due to simple construction.
Flexibility: Provides good flexibility and easy installation in medium-pressure applications.
Durability: Provides reliable performance for environments where pressure requirements are not high.
Wide availability: Common and widely used in various industries, so it is easy to find replacements.
Potential disadvantages and limitations of using R1 hose:
Pressure limitation: Not suitable for high-pressure applications, R2 or spiral wire hoses are more suitable.
Limited temperature range: May not perform well in extreme temperature conditions compared to hoses designed for a wider range.
Reduced strength: Monofilament braid has less reinforcement than dual-filament or spiral wire hoses, which may limit its use in high-stress applications.
Abrasion: The housing may be less resistant to certain chemicals or harsh environmental conditions, resulting in potential performance degradation over time.
SAE100 R2AT Two Steel Wire Braided Hose
SAE 100R2 High Pressure Wire Reinforced Hydraulic Hose should be used with petroleum and water based hydraulic fluids in the temperature range of -40°C to 100°C. The double wire braid reinforcement is separated by a synthetic rubber layer with a synthetic rubber cover that is oil, fuel, weather and abrasion resistant. It consists of an oil resistant synthetic rubber inner tube, steel wire reinforcement depending on the hose type, as described below, and an oil and weather resistant synthetic rubber cover. Plies or braids of suitable material may be used on the inner tube and/or on the wire reinforcement to fasten the synthetic rubber to the wire.
Double-wire braided hoses (such as R2): These hoses have two layers of wire braid for added strength and durability and are designed to handle high-pressure environments and heavy-duty applications
- Inner Tube: oil-resistant synthetic rubber.
- Reinforcement: two braids of high-tensile steel wire.
- Cover: weather- and oil-resistant synthetic rubber.
Temperature Range: -40℃ to +100℃
Main Applications: Used for conveying Medium-high pressure of oil- or water-based hydraulic fluids.
Standards: ISO 1436 R2AT, SAE J517 100 R2 type A or AT
Advantages of using R2 hose:
High Pressure Resistance: Capable of withstanding higher pressures than R1 hose, suitable for more demanding applications.
Enhanced Durability: Double braided wire provides superior strength and resistance to external damage, which extends the life of the hose.
Flexibility: Provides high pressure performance while maintaining good flexibility, allowing for easier installation in a variety of configurations.
Safety: Reduces the risk of hose failure under high pressure conditions, improving safety and reliability of operations.
Potential Disadvantages and Limitations:
Cost: Typically more expensive than R1 hose due to additional reinforcement and construction complexity.
Bend Radius: While flexible, the minimum bend radius is larger compared to R1 hose, which may limit installation in very tight spaces.
Weight: The additional wire braid adds weight to the hose, which may need to be considered in applications where hose weight is an important factor.
Temperature Sensitivity: Although the standard temperature range is wide, extreme temperatures may still affect performance, especially when the hose is exposed to conditions outside the specified range.
When to Choose R1 Hose
Medium-Pressure Applications: R1 hoses are ideal for medium-pressure (typically up to 3000 psi) hydraulic systems. They are ideal for applications where pressure requirements are modest and do not exceed the rated capacity of the hose.
Agriculture: Used in hydraulic systems of tractors and other farm equipment.
Construction: Applied to hydraulic machinery such as excavators, backhoes, loaders, etc.
Manufacturing: Used in hydraulic presses, conveyors, and other machinery.
Automotive: Found in hydraulic systems of automotive lifts and machinery.
Cost-Conscious Projects: R1 hoses are more cost-effective than high-pressure hoses due to their simpler construction with single-wire braid. R1 hoses are a good choice for projects with limited budgets but still requiring reliable performance.
Flexibility Needed: Where flexibility and ease of installation are critical, R1 hoses are designed for good maneuverability and a relatively small bend radius, making them suitable for applications with limited space or complex routing.
When to Choose R2 Hose
High-Pressure Applications: R2 hoses are designed to handle higher pressures, typically up to 5000 psi. They are essential in hydraulic systems where high pressure is often required, such as heavy machinery, construction equipment, and high-pressure industrial processes.
Construction: Essential in hydraulic machinery such as excavators, bulldozers, and cranes, as high-pressure operation is standard for these machines.
Mining: Used in mining equipment such as drills, loaders, etc. that operate under high pressure.
Oil and Gas: Applied to hydraulic systems of drills and other equipment that require high-pressure hoses.
Manufacturing: Used in hydraulic presses and heavy machinery that require higher-pressure capabilities.
Durability Requirements: When the application requires superior durability and strength, the R2 hose's double braided reinforcement layer provides increased resistance to pressure and external damage. This makes the R2 hose suitable for environments where the hose is subject to severe wear and tear.
High-Pressure Environments: For situations where operation is in harsh conditions or where the hydraulic system is subject to high pressure, the R2 hose provides better performance and safety due to its rugged construction and higher pressure rating.
Factors to consider when choosing between R1 and R2:
Pressure requirements: Evaluate the maximum operating pressure of your hydraulic system. For moderate pressure needs, choose R1; for high-pressure applications, choose R2.
R1 hoses are designed to handle moderate pressures, typically ranging from 1,000 to 3,000 psi (pounds per square inch). The exact pressure rating depends on the hose's diameter and quality of construction. It is critical to select an R1 hose that meets the pressure requirements of your hydraulic system to ensure reliable performance.
R2 hydraulic hoses can handle higher pressures than R1 hoses. Their pressure ratings typically range from 2,000 to 5,000 psi (pounds per square inch), depending on hose size and construction. This high-pressure rating makes R2 hoses suitable for more demanding hydraulic systems, which typically require high pressures.
Flexibility vs. Strength: Determine if flexibility or strength is more important for your application. R1 hoses offer greater flexibility, while R2 hoses offer greater strength and durability.
The single-wire braid construction of the R1 hose provides moderate flexibility and bend capability. The minimum bend radius of the R1 hose is typically approximately 4 to 6 times the hose diameter, depending on the size and construction of the hose. This flexibility makes the R1 hose suitable for applications that require a certain degree of movement and maneuverability.
Despite its rugged dual-wire braid construction, the R2 hose offers good flexibility. The minimum bend radius is typically approximately 5 to 8 times the hose diameter, providing a balance between strength and maneuverability. This flexibility allows installation in tight spaces while maintaining durability in high-pressure conditions.
Cost vs. Performance: Balance budget with performance needs. The R1 hose is more cost-effective but less suitable for high-pressure environments, while the R2 hose offers enhanced performance at a higher cost.
Conclusion
Choosing the right hydraulic hose is essential to ensure optimal performance and longevity of your hydraulic system. R1 and R2 hoses serve different purposes, and choosing the type of hose that suits your specific needs can have a significant impact on system efficiency and safety. Before making a final decision, consult with a hydraulic hose expert or supplier to understand your specific requirements and ensure you select the best hose for your application.