Hose Crimping Machine SNP-P32
Sinopulse have been supplying some hose crimping machines for 10 years, such as Hose Crimping Machine SNP-P32 ect. Helping you with crimping technology and OEM hoses bussiness needs. Feel free to contact us.
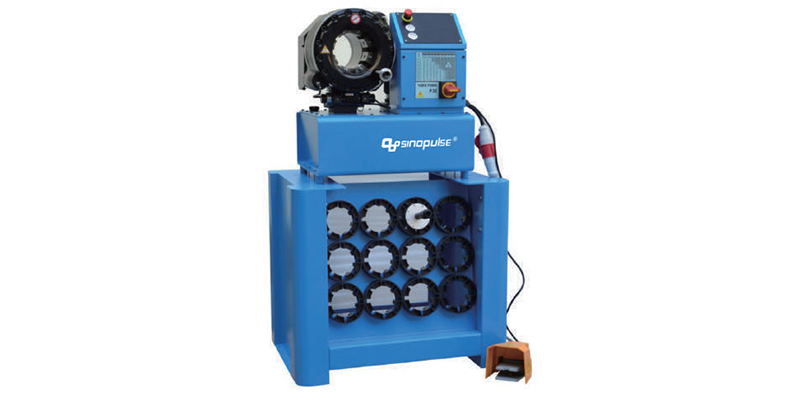
SNP-P32 hose-crimping machine has been designed to crimp up to 2" diameter 4-spiral hoses. And for workshop use. It is fast and easy to use.
TECHNICAL DATA | Details |
Max crimping dia (mm) | 10-87 |
Max crimping dia (inches) | 0.39 - 3.42 |
Max. crimping force (kN) | 2000 |
Max. crimping force (tonnage) | 200 |
Cycle time 10 mm (s) (Tri/Mono) | 3.3 / 5.5 |
Hose size ID (inches) | 2 (4SH) |
Dies set series | P32 |
Max. opening (mm) | 33 |
Max. opening without dies (mm) | 132 |
Master die D/L (mm) | 99 / 80 |
Master die D/L (inches) | 3.90 / 3.15 |
Motor Tri/Mono (kW/HP) | 3.7 / 5 (Tri), 4 / 5.3 (Mono) |
Oil tank volume (L) | 42 |
Crimping/hour | 700 / 850 |
Motor Voltage (V) (Tri/Mono) | Tri: 200/220/380/440, Mono: 220/230/240 |
STANDARD DIES
D (mm) | 14 | 16 | 19 | 22 | 26 | 30 | 34 | 39 | 45 | 51 | 57 | 63 | 69 |
L (mm) | 55 | 55 | 55 | 55 | 70 | 70 | 75 | 75 | 90 | 90 | 100 | 100 | 100 |
Crimping Range | 14-16 | 16-19 | 19-22 | 22-26 | 26-30 | 30-34 | 34-39 | 39-45 | 45-51 | 51-57 | 57-63 | 63-69 | 69-75 |
Crimping vs. Swaging: What's the Difference
Crimping and swaging are critical processes in hose assembly, regardless of the application. To adequately secure and tighten industrial hoses, it is important to understand the basic differences between crimping and swaging.
Swaging is the process of increasing or decreasing the diameter of a tube along a portion of its length. This is usually a cold working process.
Crimping is the process of reducing the diameter of a pipe so that it can be snapped onto another pipe, securing it by deforming the second pipe. This is usually done using a crimping machine.
The Crimping Process
Crimping is a method of joining two metals together, and is usually done with a handheld tool.
Hose crimpers are used to connect deformable metal fittings with flexible hoses.
The crimping process can be done with both powered and non-powered tools, ranging from simple handheld devices to stand-alone machines designed for precision and high-volume operations.
To make the connection, the crimper applies force to the outside diameter (OD) with 360ยฐ contact. Typically, this compression is only applied once or at most a few times, using a rotating die to prevent bending.
Ultimately, this process changes the length and shape of the entire circumference. Because the compression occurs simultaneously, more force is required to reduce the ferrule
During the crimping process, two metals or a metal and plastic are pressed together by a single compressive force. The compressed area is deformed by the divot so that it is no longer cylindrical.
For example, crimping is used in the electrical industry to keep wires neat and to fuse wires together. Electricians will use crimping tools to crimp fittings onto wires to connect them to another wiring assembly or other wires.
Use crimping when weight requirements are not an issue.